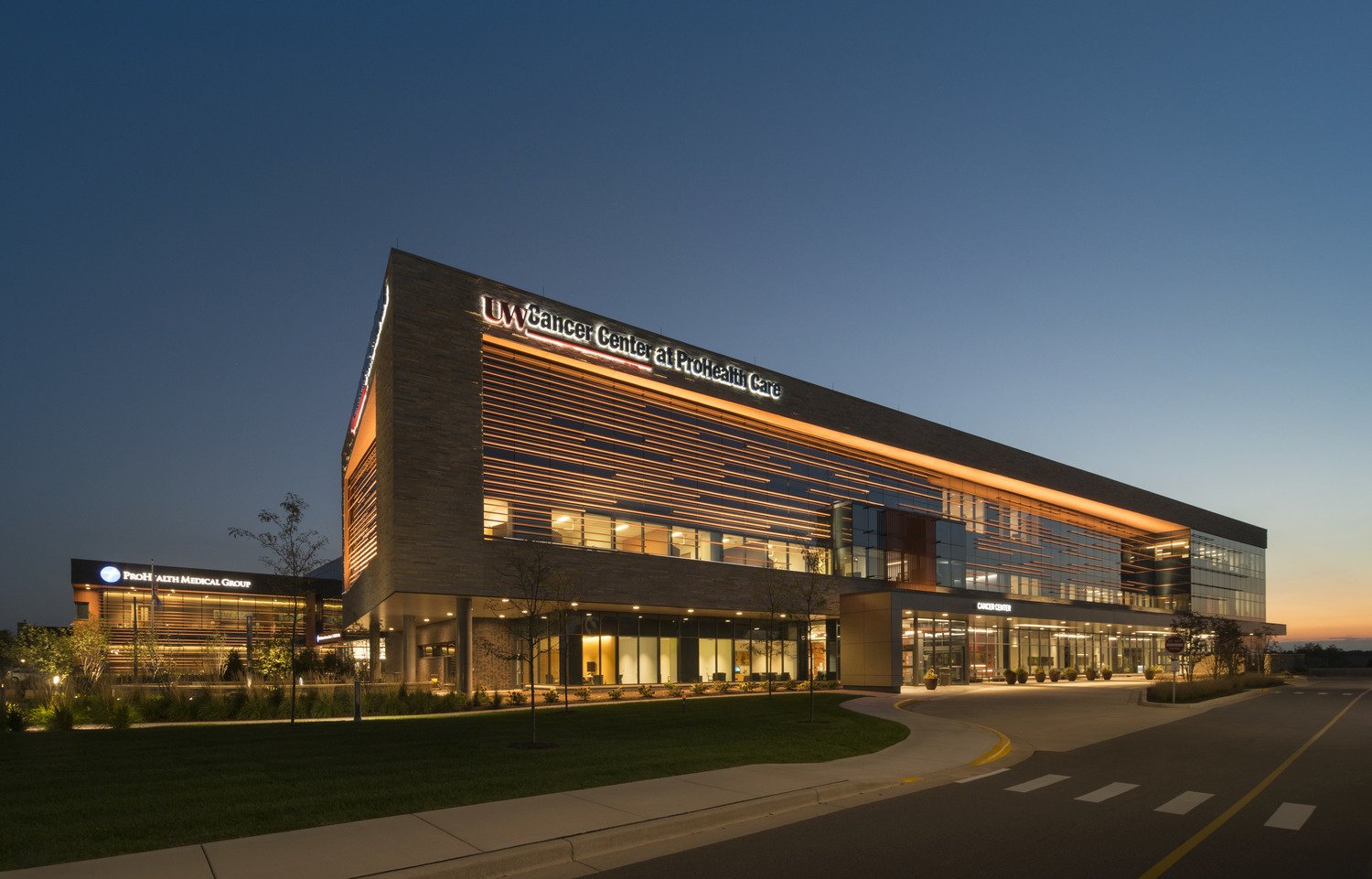
The classic look of brick meets the sustainable performance of the rainscreen system in the Brick Rainscreen System by Dasana Partners. Stainless Steel DURUS trays mark a new era of performance in brick trays. The Durus I System is a fully engineered brick rainscreen system with rear ventilation, open cavity, and water management. At 12lbs. per square foot this system is lighter, quicker and easier to install, and meets all of the latest energy codes including ASHRAE 90.1 and latest stretch code adaptions. This system will last as long as the wall is upright.
Our parent company, Belden Tri-State Building Materials, is the leading supplier of brick and thin brick products in the region. To see a vast array of compatible brick options for the Brick Rainscreen system, see here.
The Innovative DURUS™ System
-
20-gauge 304B stainless steel eliminates all concerns regarding corrosion or rust. Weep holes are standard across the backside lower edge assuring all incidental moisture can easily escape and run down the back of the trays and through the cavity. Stiffener ribs reinforce the structural strength of the tray and also serve as guides to assure vertical alignment. Brick will set along the uniform bottom edge of the tray to keep the horizontal alignment uniform. The spacing between each tray can be adjusted if necessary to help align with rough openings in the wall.
-
DURUS trays from Desana Partners are also available in galvanized steel. They are produced according to ASTM A653 which is the specification for sheet steel, zinc coated, using the continuous hot dipped process. This is a widely used process to coat sheet steel prior to fabrication. The coating produced by continuous galvanizing is uniform, has sufficient ductility to withstand deep drawing or bending without damage to the coating, and consists almost entirely of pure zinc.
-
DURUS trays are coated using the continuous hot dipped process prior to fabrication. During fabrication trays are punched, formed, and cut to length. Trays may also be cut to fit in the field or on site. All of these processes will leave exposed edges of uncoated steel. In terms of cathodic protection offered by a galvanized coating of adequate thickness to a bare area, the two most important variables are the width of the bare area and the electrolyte that connects the galvanized coating and bare area. Due to the variability in electrolyte properties, it is hard to give exact widths of bare areas on galvanized steel that will be cathodically protected, but various studies have found in atmospheric exposure in urban environments, bare areas up to 2 millimeters in width will be completely protected. DURUS trays are made of 20-gauge steel and should be well within the estimated cathodically protected area.
-
Care is taken to allow for as much egress of water and moisture management as possible. The environment for the system and in particularly the trays is at times, wet, damp, or dry. With a typical rainscreen assembly there will be a continuous convection air flow within the cavity to keep components as dry as possible. Each tray has uniform and continuous drainage holes and fixing holes that will provide for maximum egress of moisture and water. We expect very little water or moisture to collect and remain within the trays.
Sub-Framing Systems
-
Full Rainscreen Assembly
A full rainscreen system begins with an air/moisture barrier directly to the substrate. Our thermally isolated brackets are attached through the barrier and into the structural wall. Insulation is placed over the brackets. Brackets come in depths from 2” - 10” deep, to allow for greater thicknesses of insulation and an open cavity depth of two inches. Vertical L profiles are fixed to the brackets. The specially designed brackets and profiles allow the installer to plane out the wall and eliminate substrate irregularities before the first tray is installed. Trays are mounted to the vertical profiles and bricks are inserted into the trays.
-
Cavity System
In cases where the full rainscreen system is not required simple Z profiles can be installed onto a watertight substrate creating a cavity area of for 1”to 3”. This cavity will help to eliminate any moisture buildup behind the system.
-
Direct Applied
When budgets are tight it is also possible to install the Durus trays directly to a watertight substrate. Bricks can be installed to the trays and mortared accordingly.